Many 3D printers are either expensive and have high performance or have low cost and low performance. I am building a testbed for 3D printing and the goal is to combine high performance with low cost by using sheet metal and low cost electronics instead of machined parts and industrial PLC. Servos are replacing stepper motors and ground screws are replacing belts. Why? Because 3D printing is a slow process and in order to use it for volume manufacturing the investment must be kept low but the performance has to be high. I will use FDM (or FFF) since it is the most widely used process with many available sub systems on the market and in the open domain. The same principles could be used for other processes, for example ink-jet on metal powder bed which is my speciality.
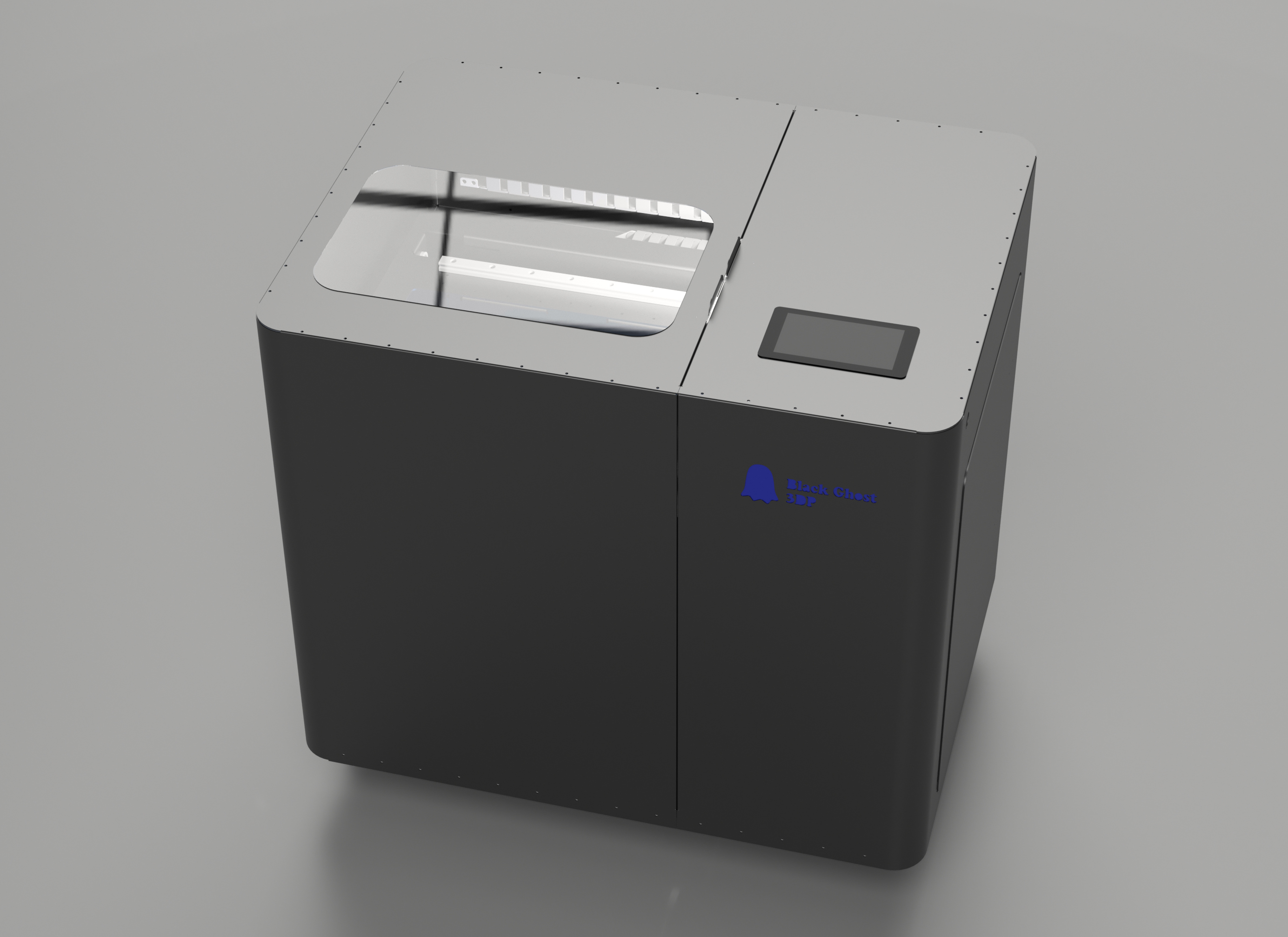
Properties of the machine
300 x 500 mm build area to enable larger parts like jigs and fixtures or multiple parts in one build. The kinematic is cartesian.
Sheet metal design for low cost and producibility. Sheet metal can be really cost efficient compared to machined parts if made in volume around 50 or more.
High torque servos for speed AND precision. Steppers and stepper drivers are becoming better and have a lower price compared to servos. But servos are also evolving and the cost is slowly moving toward the stepper . The performance of a servo is always better than a stepper since it can combine low energy consumption (low heat generation), high torque at high rpm and closed loop control to keep track of its position. SimplexMotion for example is making servos from drone motors and with volume this could be a really attractive solution.
Ground screws with high lead for speed, precision and stiffness. There are two alternatives for a fast movement with precision, servo with screw or a linear motor. Belts that are used for most low cost 3D printers do not have the accuracy, stiffness and temperature stability that is required for a high precision machine, but the cost is low. Linear motors are today too expensive, but otherwise have a good fit for 3D printing where the loads are low and speed can be high. I therefore think that the screw solution has the best fit. Once this decision is made you have to choose the type of nut. There are zero-backlash plastic nuts that probably would work if the load is low, but will wear over time. I have chosen a short steel nut with steel balls and a ground screw. Why a ground screw and not a less costly rolled? In my experience a ground screw will generate less noice at high rpm, and that is an important factor.
Pre-tensioned ball linear guides for precision and stiffness. Ball linear guides are quite affordable today and by using a 20 mm rail the weakness of the sheet metal is compensated.
1000 mm/s max speed for rapid moves and uninterrupted nozzle flow. Keeping the flow in the nozzle uninterrupted makes it easier to control the extrusion. This makes it easier to move the hot-end quickly from island to island with minimum delay.
2 g acceleration and high jerk for constant pressure extrusion. By having the possibility to move the hotend at a constant speed the conditions can be kept unchanged. The capability to accelerate quickly is therefore vital. This will lead to that the calibration of the process is simpler and more reliable and has better accuracy and repeatability of the printed parts. A bonus is that the print time will be reduced which improves the productivity.
Two build materials from two separate extruders that can be elevated separately to avoid nozzle drag and ooze. One build material and one soluble support material makes it possible to build most parts and simplify the cleaning of the support.
Ruby nozzles and all metal hot-end for high temperatures and long life when using abrasive materials. The use of carbon fiber reinforced materials has a rapid adoption on the market and makes it feasible to build functional parts like jigs and fixtures that can withstand high loads. To resist the wear from the carbon fibers hard materials in the nozzle is required. One good solution that I will use is the Olsson Ruby.
Service area for hot-ends with cleaning and priming. Some, if not all, plastic materials that have been kept hot will deteriorate. Having the possibility to clean this out before starting to print will help improve the quality of the printed parts. A soft brass brush will be used to clean the nozzle.
Pt100 temperature sensors for reliable measurement of high temperatures. Many 3D printers use thermistors for temperature measurement since they have a very low cost, but they have poor accuracy and a limited temperature range. An other alternative is thermocouples but they require uninterrupted wires from the measurement point to the A/D converter. A Pt100 will be used in the machine since it has a wide temperature range and the resolution of the temperature readout is high.
Heated build chamber to reduce warping and enable more materials. The possibility to keep the heated part warm during the build process will reduce the temperature difference in the part and reduce the internal residual stresses that can cause cracks after the build is finished and during use. The temperature cannot be too high because the plastic can start to deteriorate, something I have observed in some high end printers.
Dual drive extruders from Bondtech for reliable high pressure extrusion. Bondtech has developed an extruder that is reliable and can push filaments with a high force without grinding. This is achieved by driving the filament on two sides. This is vital to achieve a reliable and predictable extrusion.
A 32-bit controller with touch display for higher step rates and better performance. The trend is towards more powerful controllers which have a low cost. At some point these controllers have the capability to replace industrial PLC's with a much higher price. For this application I believe the time has come so I will use custom electronics.
Wi-Fi connected and web browser interface for simple monitoring and control. The controller electronics has to be able to support web access over WiFi without being interrupted. Ideally an FPGA should be used for step and direction control, but this is not the case right now.
Supported by all slicers for freedom of choice. There are many slicers today that can generate high quality G-code files. All of them can be used.
Planned for carbon fiber reinforced polyamide (nylon) and metal filament like BASF Ultrafuse 316LX. There are two trends today that is supported by user needs, high strength functional plastic parts and metal parts. There are several options for carbon fiber in a polyamide matrix and some promising development for metals. I have evaluated BASF Ultrafuse 316LX and it has a high content of steel, 53.7%, that is necessary to obtain a fully dense sintered part. Most news about the filament is from summer 2017 and BASF is not making much marketing, so I am not sure what the future is of the filament. 316L also requires an expensive furnace and most prototypes would benefit from a more cost efficient material.